Rethink Injection Molding with Low Pressure Solutions
Transform your molding process with lower pressure, greater efficiency, and unmatched protection for delicate components.
Injection Molding vs. Low Pressure Molding
Which Process is Right for You?
Low Pressure Molding Compared
to High Pressure Injection Molding
High Pressure Injection Molding | Low Pressure Molding | |
Pressure | 25,000 PSI | 100 PSI |
Temperature | 185–300+°C | 180–220°C |
Material Viscosity | 5 grams over 10 min Melt Flow Rate
• Taffy
|
2,000–10,000 mPa•s (cP)
• Pancake syrup
|
Applications |
• PCB Housings
• Tooth Brushes
• Bottle Caps
• Pocket Combs
• Plastic Parts
|
• PCBs
• Sensors
• Switches
• Batteries
• Connectors
|
Equipment | Injection Molding Machine
• Screw barrel system
|
Low Pressure Molding Machine
• Gear pump system
|
Clamping Pressure | 28–1,000 tons | 1–10 tons |
High Pressure Injection Molding | |
Pressure | 25,000 PSI |
Temperature | 185–300+°C |
Material Viscosity | 5 grams over 10 min Melt Flow Rate
• Taffy
|
Applications |
• PCB Housings
• Tooth Brushes
• Bottle Caps
• Pocket Combs
• Plastic Parts
|
Equipment | Injection Molding Machine
• Screw barrel system
|
Clamping Pressure | 28–1,000 tons |
Low Pressure Molding | |
Pressure | 100 PSI |
Temperature | 180–220°C |
Material Viscosity | 5 grams over 10 min Melt Flow Rate
• Taffy
|
Applications |
• PCB Housings
• Tooth Brushes
• Bottle Caps
• Pocket Combs
• Plastic Parts
|
Equipment | Injection Molding Machine
• Screw barrel system
|
Clamping Pressure | 28–1,000 tons |
How Low Pressure Molding
Outperforms Injection Molding
Why Low Pressure Molding
Is a Better Choice
Compared to high pressure injection molding, Low Pressure Molding offers unique advantages that make it an ideal choice for modern manufacturing:
Protects delicate components
Sustainability
Flexibility
Cost-effectiveness
See How Low Pressure Molding
Makes a Difference
A comparison between traditional high pressure injection molding and low pressure molding shows how LPM provides unique advantages. With its ability to operate at lower pressures and reduce cycle times, LPM offers an efficient and protective solution for delicate components. Unlike traditional methods, LPM optimizes injection processing by reducing complexity and minimizing stress on sensitive parts. Watch our video to learn more about these benefits and explore how LPM meets modern manufacturing challenges.
VIDEO
Protect with Low Pressure Molding – it’s that simple
FAQ
Injection Molding & Low Pressure Molding
What is high pressure injection molding?
What are the steps in the injection molding process?
How does Low Pressure Molding differ from injection molding?
Low Pressure Molding operates at significantly lower injection pressure compared to injection molding, making it ideal for sensitive components like PCBs and connectors. In addition, it simplifies manufacturing for delicate applications by avoiding the need for traditional high pressure injection machine processes.
What materials can be processed with injection molding and Low Pressure Molding?
Which industries use injection molding and Low Pressure Molding?
How sustainable is Low Pressure Molding compared to injection molding?
LPM is more sustainable, requiring less energy, producing minimal waste, and supporting eco-friendly materials.
How can I determine if Low Pressure Molding is right for my application?
LPM is more sustainable, requiring less energy, producing minimal waste, and supporting eco-friendly materials.
LPMS USA
Equipment & Materials
Low Pressure Molding Equipment
Equipment
Low Pressure Molding Materials
Materials
LPMS USA offers an extensive portfolio of low pressure molding materials
Sustainability
in Low Pressure Molding
Discover how Low Pressure Molding reduces energy consumption, minimizes waste, and supports a circular economy with sustainable materials.
LPMS USA Brochure
Explore our comprehensive brochure and discover more about our low-pressure injection molding offerings, including equipment, materials, and services. Learn how LPMS USA can benefit your production needs.
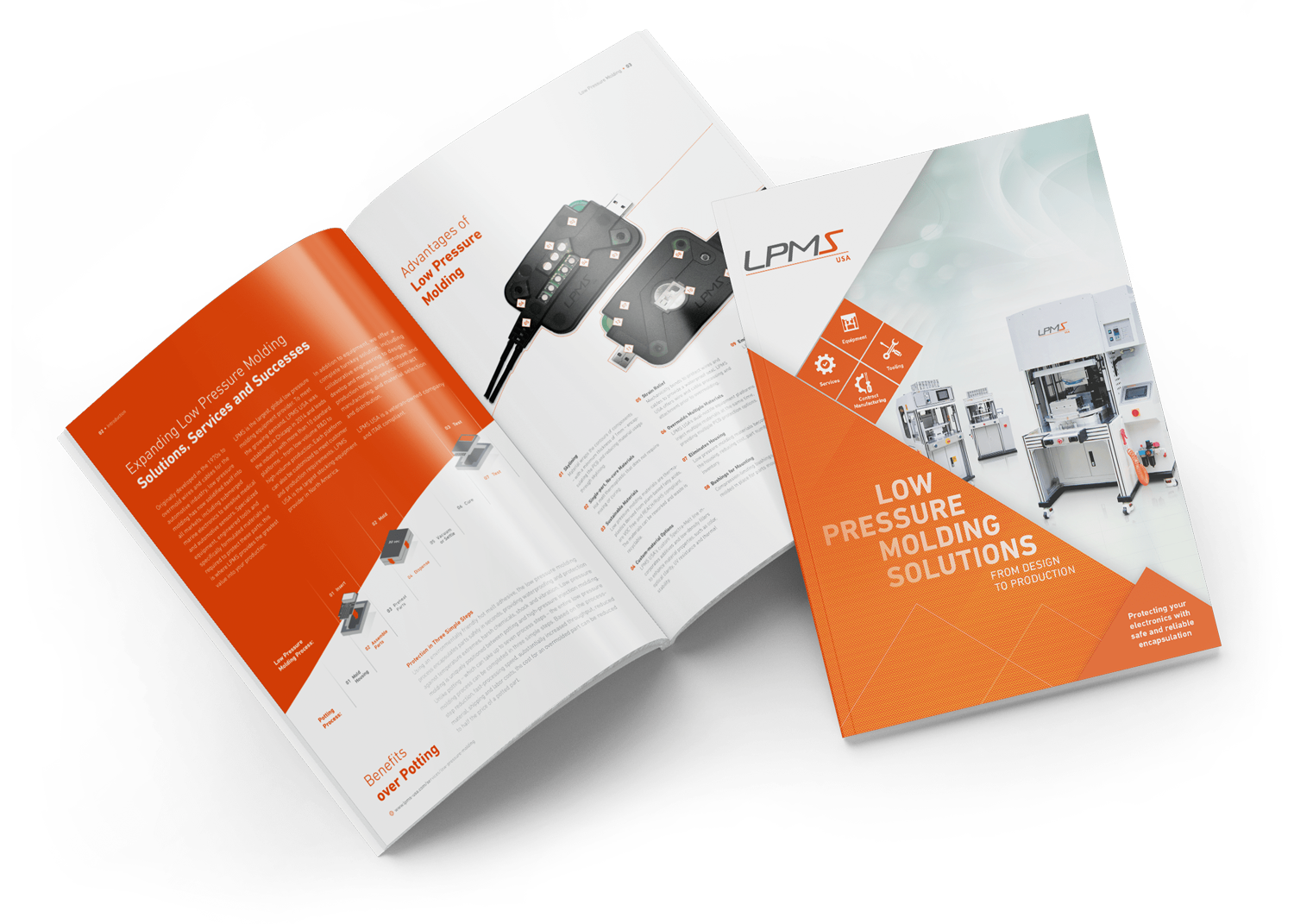
Tooling Services
Reliable, Repeatable Tooling
Overmolding Services
Contract Manufacturing
LPMS USA is the only low pressure molding equipment provider with its own ISO 9001-certified and ITAR registered and compliant production facility
Low Pressure Molding
Technology Overview
Unlike potting and other encapsulation techniques, the entire low pressure molding process can be completed in three fast, simple steps
Further Topics
Cost Savings Calculator
Our low pressure molding solutions open up great savings opportunities for you. Use our cost savings calculator to identify your individual savings potential.
Get in Touch
LPMS USA
1441 Branding Lane, Suite 110
Downers Grove, IL 60515 USA
Tel: +1 (800) 353-7773
Application Checklist
Tell us about your project, and an LPMS USA representative will contact you directly